Automation1 FLEX Distributed Amplifier Multi-Axis Servo Control System
Want a sleeker, more innovative design for your Aerotech custom-engineered motion system? Add Automation1 FLEX, which reduces cabling by distributing up to four axes modules on your mechanical stages.
Description
Specifications
Dimensions
Downloads
Description
Description
Specifications
Dimensions
Downloads
Description
Key Features
- Daisy-chain signals to minimize cable management
- Field-mounted axes modules reduce cabinet space
- Centralized flex controller connects to 4 axis modules
- Axes modules include power amplifiers & feedback signal processing
- Low-latency serialized axis feedback
- High-flex glass optical fiber cables
- Works with encoder-based position synchronized output (PSO)
Control Without Compromise
Want a sleeker, more innovative design for your Aerotech custom-engineered motion system? Add Automation1 FLEX, which reduces cabling by placing up to four axes modules on your mechanical stages. These modules include your power amplifier and axis feedback signal, enabling complete serialization of your power supplies and axis feedback for a multi-axis custom motion system. The axis feedback runs over the durable high-flex glass optical fiber Hyperwire FLEX network. The protocol enables a low latency, high-speed path that enables encoder-based PSO over a serialized feedback network.
The FLEX control system requires only a single panel-mounted controller, enabling smaller control panels and more elegant, compact machine designs. FLEX stands out in cleanroom applications, since fewer cables produce fewer particulates.
Key Applications
The FLEX is a part of the user-friendly Automation1 motion control platform, which includes the following:
Cleaner and Sleeker Design
Hyperwire FLEX delivers motion control to customers cleaner than ever before. The high-flex design separates the amplifier from the controller, enabling you to daisy chain the stage amplifiers together. This reduces drag and cable management under a new and novel low-latency design. The Hyperwire FLEX delivers key features including real-time PSO handling. Hyperwire FLEX is perfect for gantry designs and systems with up to 4 axes of motion. Hyperwire FLEX’s compact drive and cabling design makes it perfect for any system design concerned about cabinet space, cable drag, or particulate generation.
Move With Confidence
Hyperwire FLEX cabling offers a durable low-latency cabling system with a 30mm bend radius. With Hyperwire FLEX’s new technology, the cables in your systems can be serialized: cleaning up your design while still achieving the high-speed and low latency standard in Aerotech products. Cleaning up your cable design improves your mechanics further, reducing both cable drag and particulate generation. Automation1 FLEX’s 4 axis controller design also reduces your cabinet space, giving you room to add to your design or reduce system footprint.
Category |
Specification |
Maximum Supported Number of Axis Modules | 4 |
Control Supply | 24 VDC |
Motor Supply(1) | Single-phase 0-240 VAC; 50/60 Hz |
Bus Supply Voltage(1) | 0-340 VDC |
Position Synchronized Output (PSO) | Standard: • One-axis PSO (includes one-axis Part-Speed PSO) Optional: • Two-axis PSO (includes two-axis Part-Speed PSO) • Three-axis PSO (includes three-axis Part-Speed PSO) • Two-axis Part-Speed PSO only (includes one-axis PSO) • Three-axis Part-Speed PSO (includes one-axis PSO) |
HyperWire FLEX Connections | 1x HyperWire FLEX Port |
HyperWire Connections | 2x HyperWire small form-factor pluggable (SFP) ports |
Sync Ports | 2x Sync Ports |
I/O Expansion Boards (Optional) | • 1x additional PSO connection point • 16x digital inputs, optically isolated • 16x digital outputs, optically isolated • 3x analog inputs, 16-bit, differential, ±10 V • 3x analog outputs, 16-bit, single-ended, ±10 V |
Internal Motor Supply Capacitance | 2400 μf |
Maximum Motor Supply External Breaker | 20 Amp (Type-D) |
Automatic Brake Control | With Automation1 Studio, a discrete digital output must be configured as the automatic brake control output. This requires the -EB1 expansion board on the FLEX Controller. You must wire the axis brake directly from the FLEX Controller (an additional device may be required). |
Drive Array Memory | 67.1 MB (16,777,216 32-bit elements) |
High-Speed Data Capture | Yes (Limitations apply. See controller help files for more information.) |
Safe Torque Off (STO) | Please contact Aerotech. |
Current Loop Update Rate | 20 kHz |
Servo Loop Update Rate | 10 kHz |
Operating Temperature | 0 to 40 °C |
Storage Temperature | -30 to 85 °C |
Weight | 1.18 kg (2.60 lb) |
Compliance | CE approved, UKCA approved, NRTL safety certification, EU 2015/863 RoHS 3 directive |
Feature |
-10 |
-25 |
Motor Style | Brushless, brush, voice coil, stepper(1) | Brushless, brush, voice coil, stepper(1) |
FLEX Controller-Side Connections: Control Supply | 24 VDC | 24 VDC |
FLEX Controller-Side Connections: Bus Supply(2) | 0-340 VDC | 0-340 VDC |
FLEX Controller-Side Connections: HyperWire FLEX Connections | 2x HyperWire FLEX Ports | 2x HyperWire FLEX Ports |
Axis-Side Connections: Motor Supply | 0-340 VDC, 4-pin high-powered D-sub connector | 0-340 VDC, 4-pin high-powered D-sub connector |
Axis-Side Connections: 25-Pin Motor Feedback Connector | - Primary encoder inputs - Auxiliary encoder inputs - Hall effect sensor inputs (A, B and C) - Thermistor motor temperature input (accepts digital) - Encoder fault input - CW and CCW limits |
- Primary encoder inputs - Auxiliary encoder inputs - Hall effect sensor inputs (A, B and C) - Thermistor motor temperature input (accepts digital) - Encoder fault input - CW and CCW limits |
Motor Supply Input Current at Full Output Power | 5 A | 10 A |
Peak Output Current (1 sec)(5,6) | 10 A | 25 A |
Continuous Output Current(5,6,7) | 3.5 ARMS | 5.3 ARMS |
I/O Port | Not yet available. Provisions exist to add I/O on a FLEX Axis Module. Please contact Aerotech for more information. | Not yet available. Provisions exist to add I/O on a FLEX Axis Module. Please contact Aerotech for more information. |
Multiplier Options | MX0 Option: Primary Encoder: 40 million counts-per-second square-wave input Auxiliary Encoder: 40 million counts-per-second square-wave input MX2 Option: Primary Encoder: 450 kHz sine-wave input, encoder multiplier up to 65,536 Auxiliary Encoder: 40 million counts per second square-wave input MX3 Option: Primary Encoder: 450 kHz sine-wave input, encoder multiplier up to 65,536 Auxiliary Encoder: 450 kHz sine-wave input, encoder multiplier up to x16,384* *Encoders multiplied with this input cannot be echoed out. |
MX0 Option: Primary Encoder: 40 million counts-per-second square-wave input Auxiliary Encoder: 40 million counts-per-second square-wave input MX2 Option: Primary Encoder: 450 kHz sine-wave input, encoder multiplier up to 65,536 Auxiliary Encoder: 40 million counts per second square-wave input MX3 Option: Primary Encoder: 450 kHz sine-wave input, encoder multiplier up to 65,536 Auxiliary Encoder: 450 kHz sine-wave input, encoder multiplier up to x16,384* *Encoders multiplied with this input cannot be echoed out. |
Absolute Encoder | BiSS C Unidirectional; EnDat 2.1; EnDat 2.2; SSI | BiSS C Unidirectional; EnDat 2.1; EnDat 2.2; SSI |
Automatic Brake Control | See FLEX Controller specifications. | See FLEX Controller specifications. |
Operating Temperature | 0 to 40 °C | 0 to 40 °C |
Typical Total Power Dissipated by Axis Module(8) | 25W @ 160 VDC 35W @ 320 VDC |
25W @ 160 VDC 35W @ 320 VDC |
Storage Temperature | -30 to 85 °C | -30 to 85 °C |
Weight | 1.18 kg (2.60 lb) | 1.18 kg (2.60 lb) |
Aerotech Stage Integration | Based on size and thermal considerations, the FLEX axis can be installed on the following Aerotech semi-standard gantry designs: AGS1000, AGS1500, AGS10000, AGS15000. Based on size and thermal considerations, the FLEX axis can be installed on the following Aerotech PRO stages: PRO225, PRO280, PRO560. For other (specifically smaller) stages, the FLEX axis module heat dissipation may be of greater concern. Please consult with Aerotech for design considerations. |
Based on size and thermal considerations, the FLEX axis can be installed on the following Aerotech semi-standard gantry designs: AGS1000, AGS1500, AGS10000, AGS15000. Based on size and thermal considerations, the FLEX axis can be installed on the following Aerotech PRO stages: PRO225, PRO280, PRO560. For other (specifically smaller) stages, the FLEX axis module heat dissipation may be of greater concern. Please consult with Aerotech for design considerations. |
Compliance | CE approved, UKCA approved, NRTL safety certification, EU 2015/863 RoHS 3 directive | CE approved, UKCA approved, NRTL safety certification, EU 2015/863 RoHS 3 directive |
Category |
|
Physical Layer(1): Cable type | High-flex glass optical fiber |
Physical Layer(1): Cable bend radius | 30mm |
Physical Layer(1): Connectors | Small form-factor pluggable |
High-speed encoder feedback latency | 1.6 μs |
Dimensions
AUTOMATION1 FLEX CONTROLLER WITHOUT MOTOR POWER SUPPLY OR EXPANSION I/O
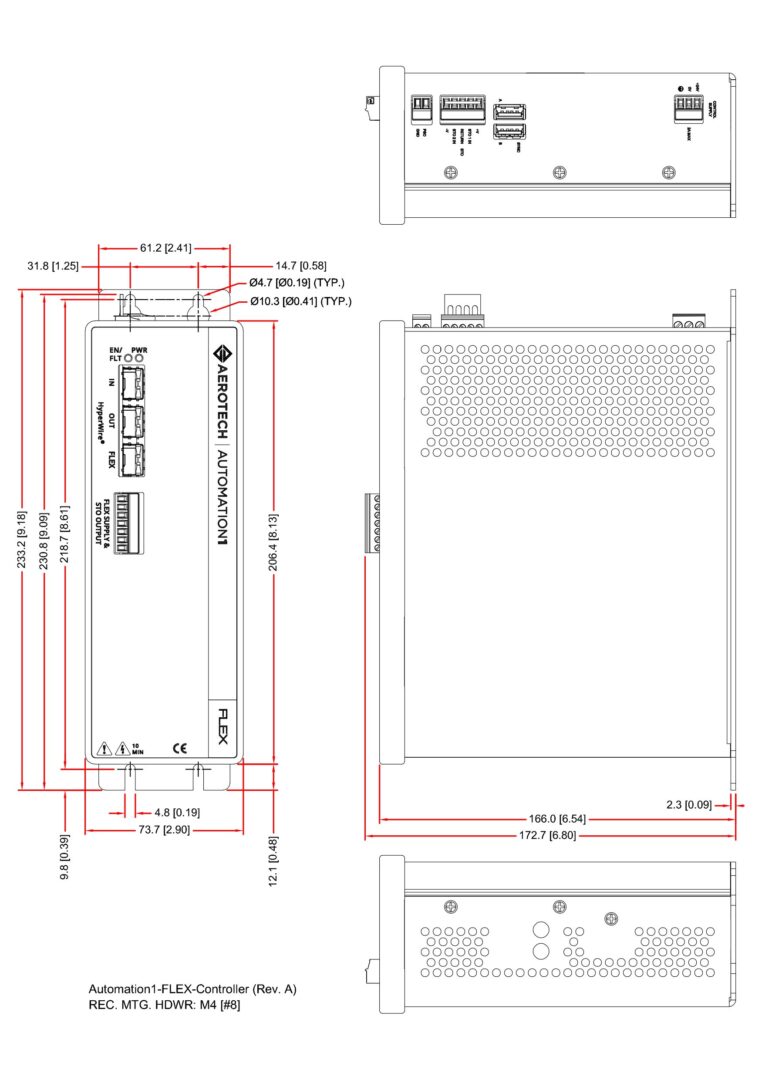
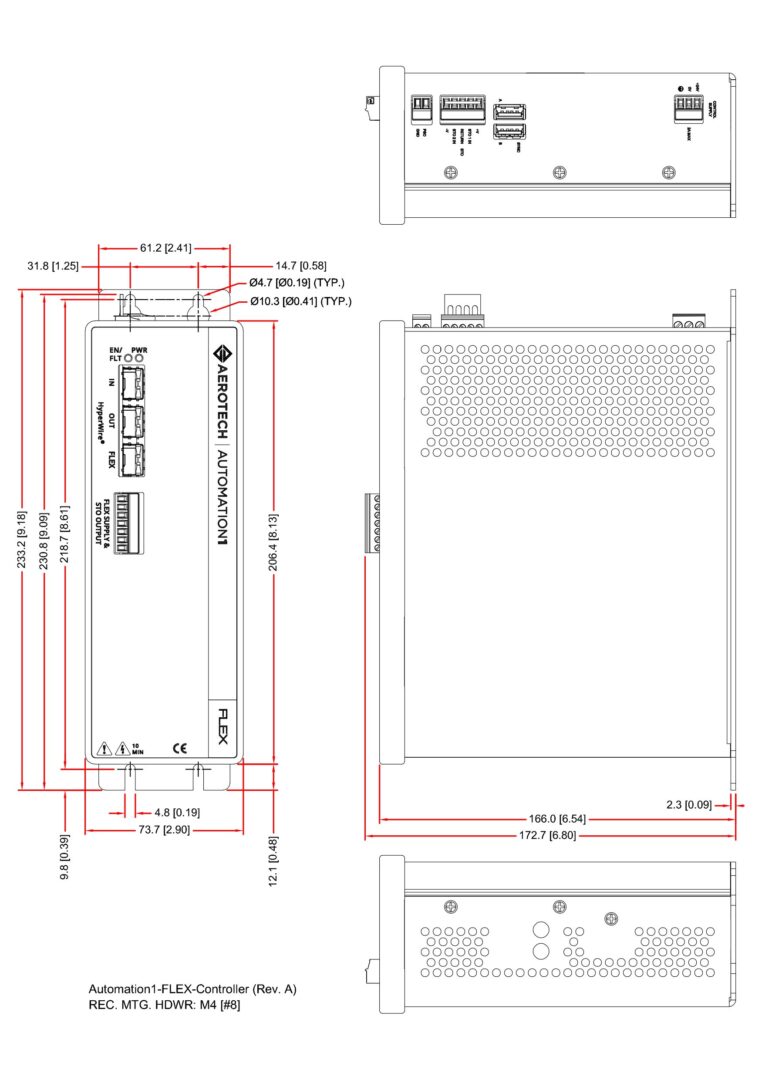
AUTOMATION1 FLEX CONTROLLER WITH MOTOR POWER SUPPLY AND WITHOUT EXPANSION I/O
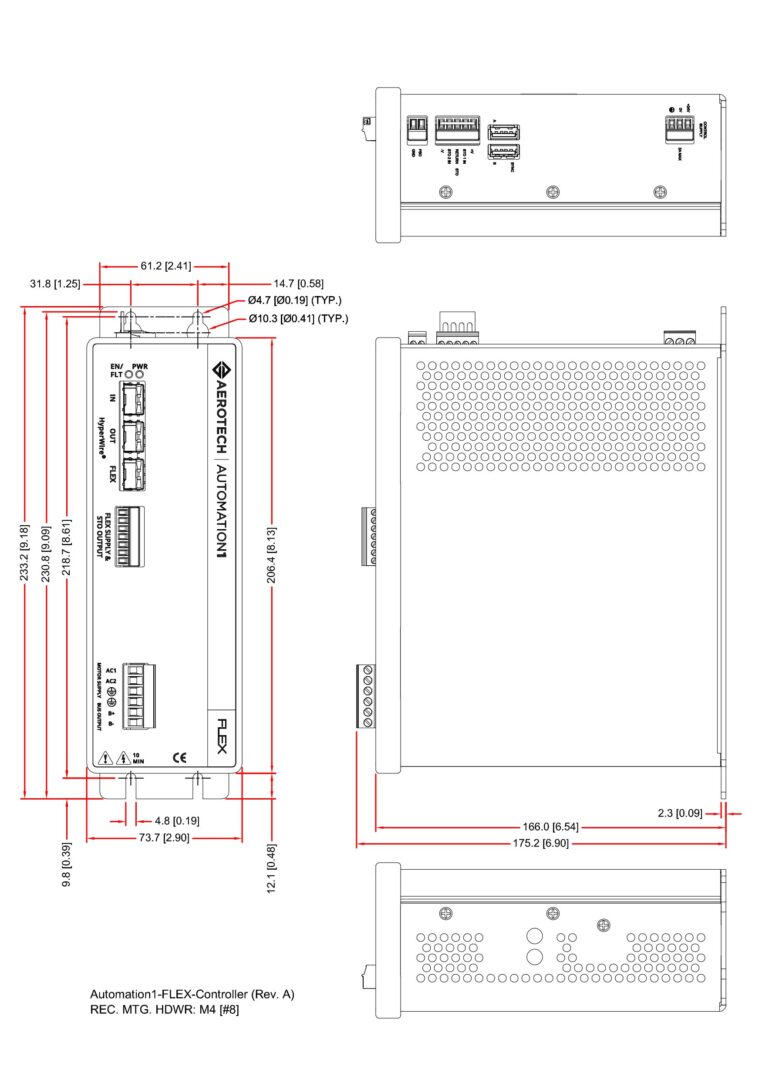
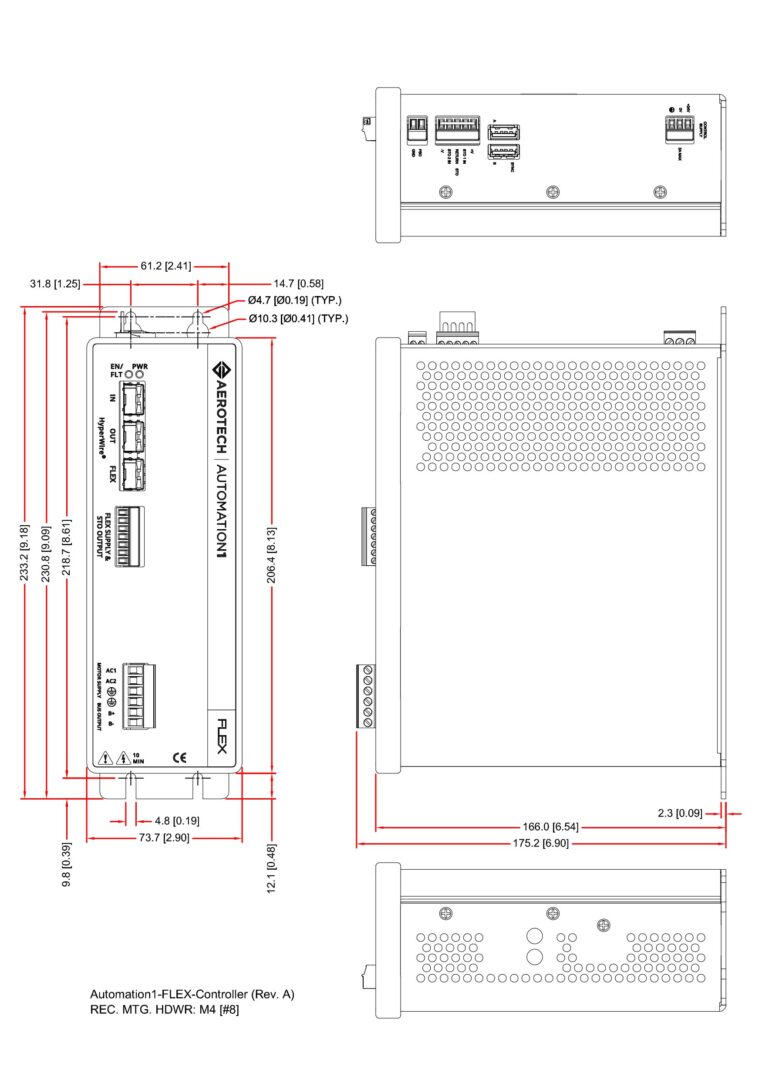
AUTOMATION1 FLEX CONTROLLER WITHOUT MOTOR POWER SUPPLY AND WITH EXPANSION I/O
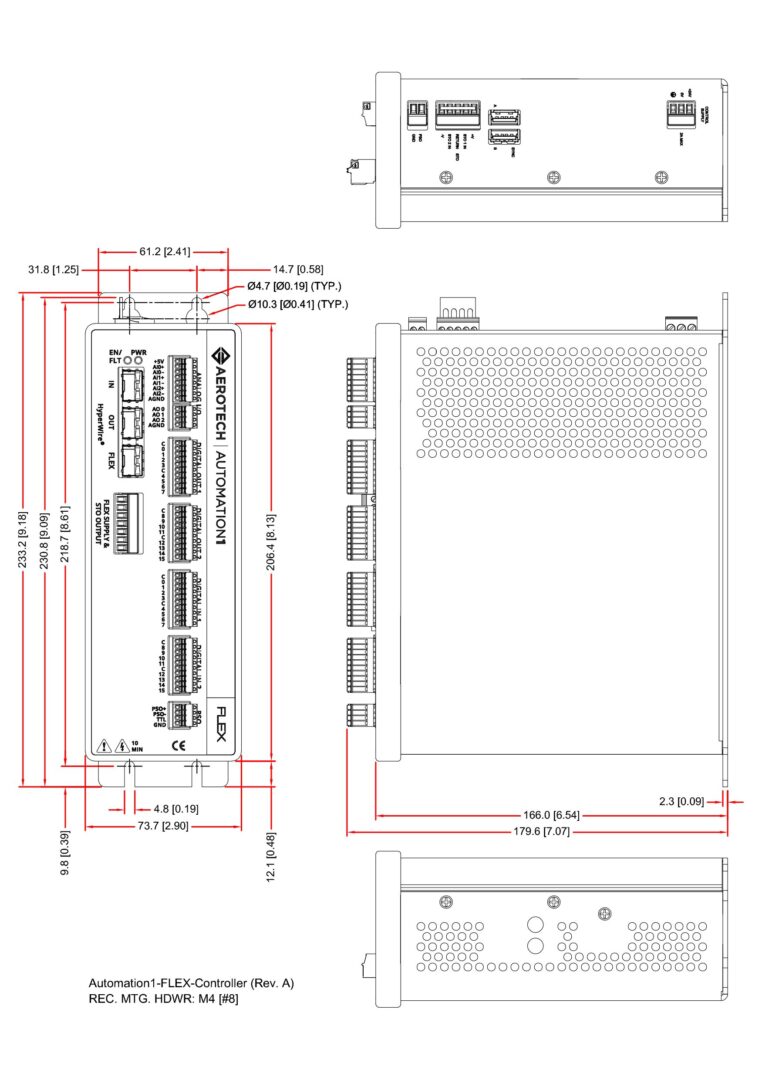
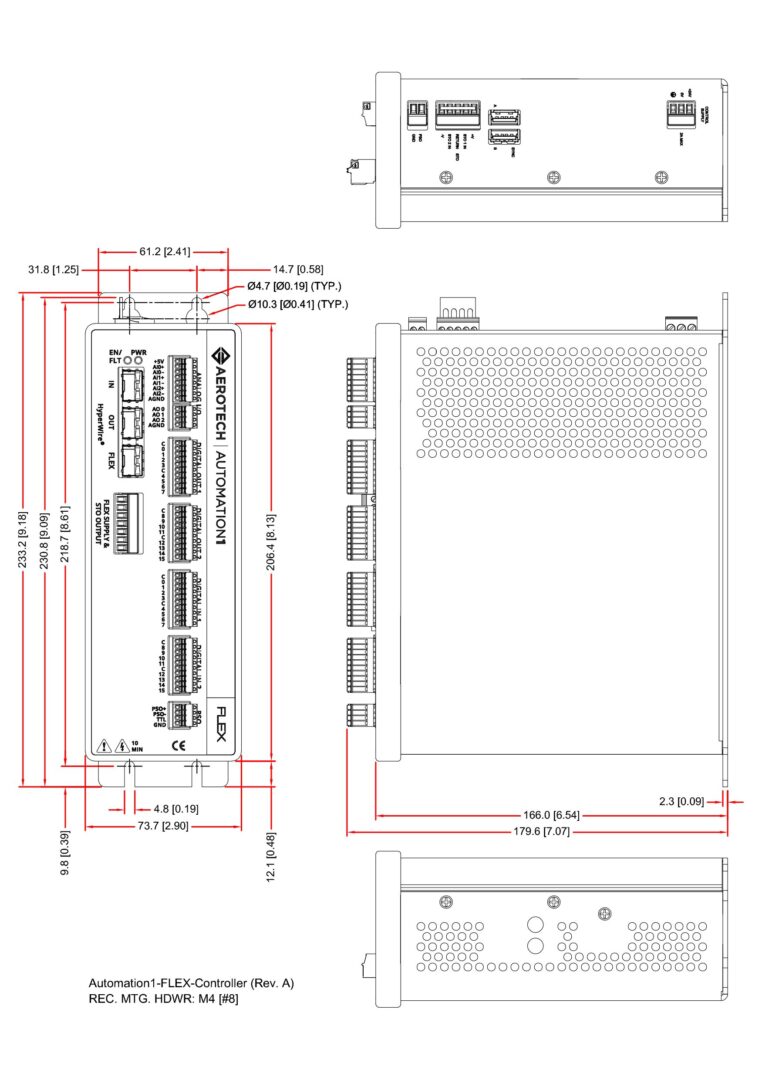
AUTOMATION1 FLEX CONTROLLER WITH MOTOR POWER SUPPLY AND WITH EXPANSION I/O
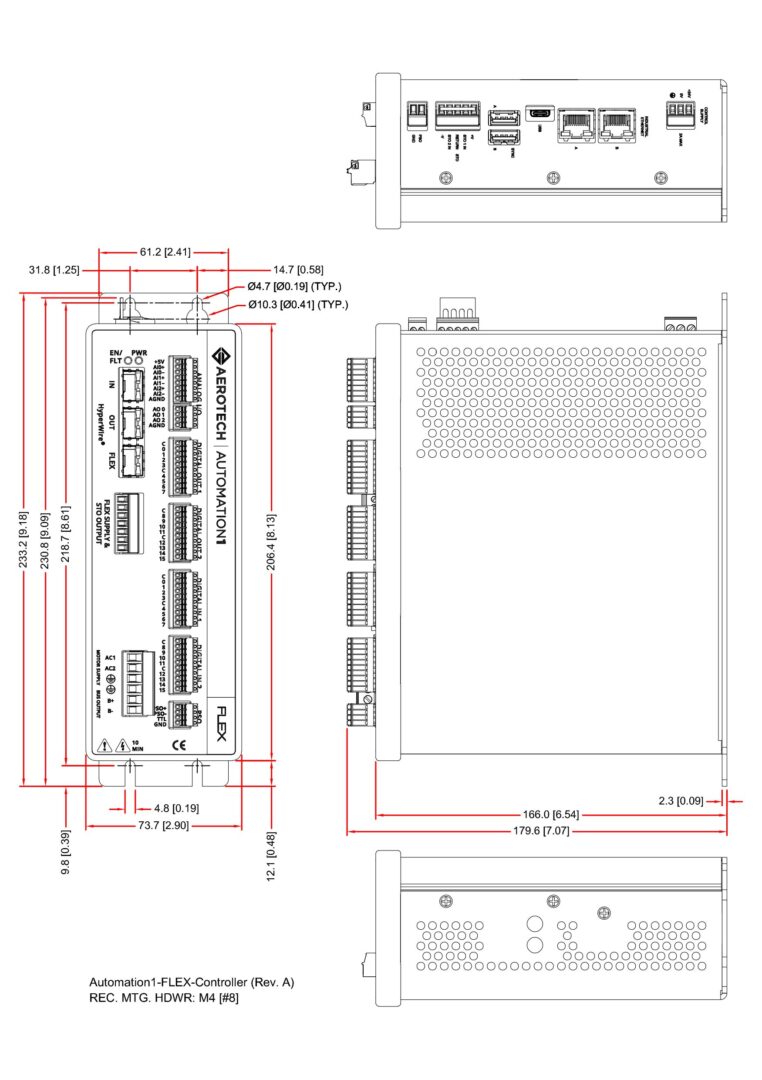
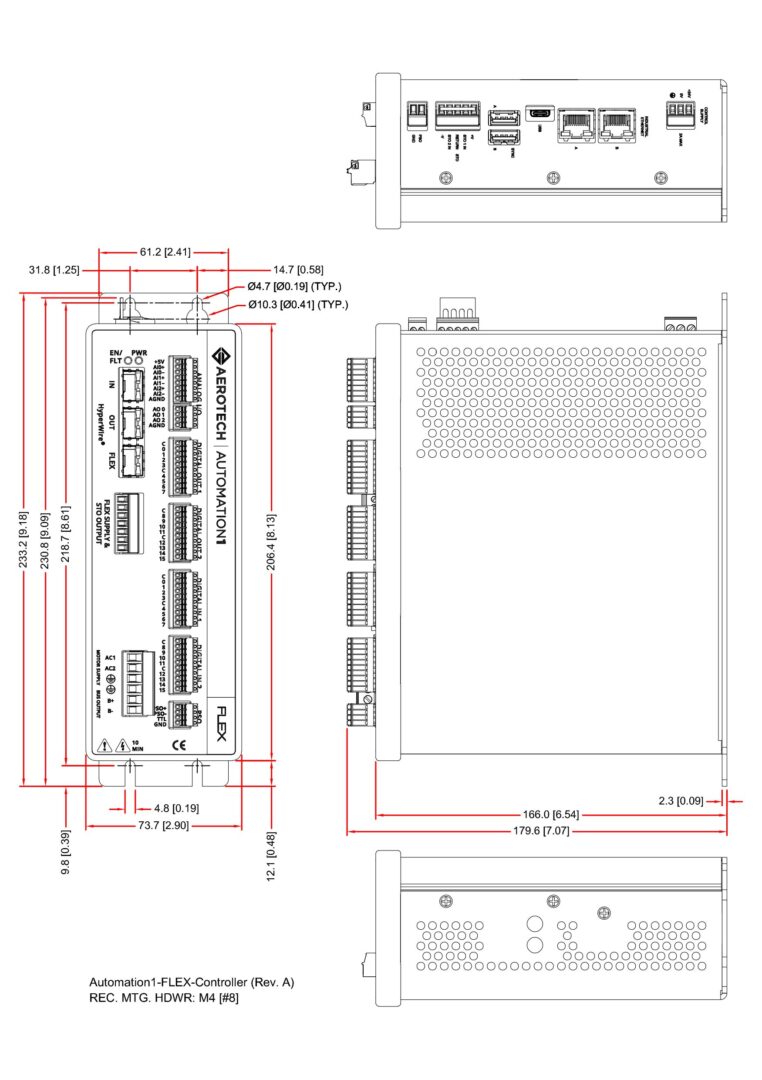
AUTOMATION1 FLEX AXIS MODULE
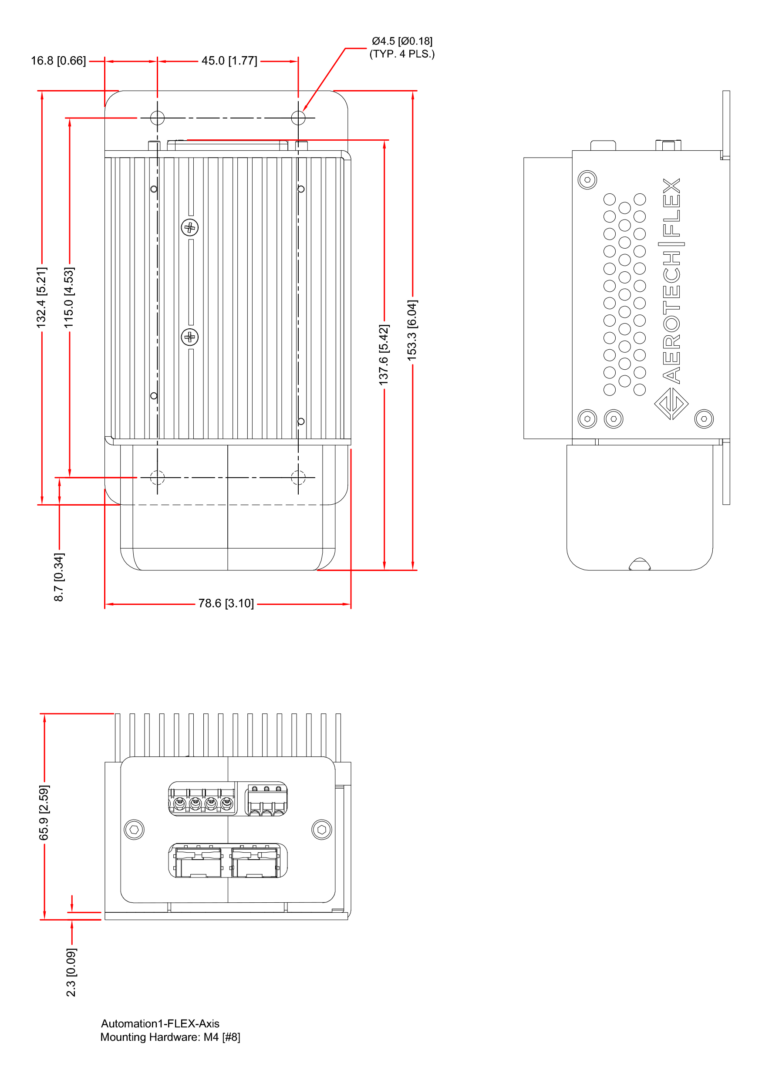
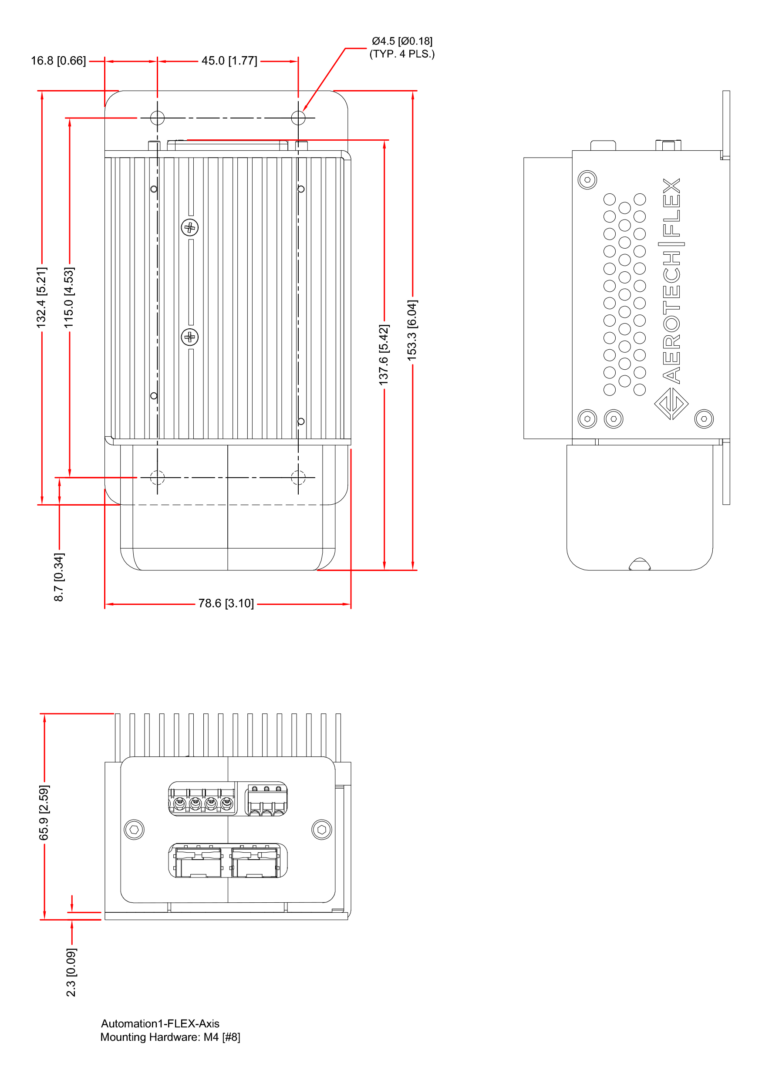