Aerospace & Defense, Capability Overview, Custom Engineered Motion Systems, Electronics, Gantries, Integrated Automation Systems, Laser Scan Heads, Laser Systems, Medical Device Manufacturing, Motion Control Platforms, Motors, Precision Manufacturing, Stages & Actuators
Capability Overview
Infinite Field of View (IFOV) Synchronizes Linear or Rotary Servo Axes with Laser Scanners
Design Features
- Easy-to-use setup parameters and effortless execution on every profile
- Real-time simultaneous trajectory generation from one controller
- Automated dynamic error correction of servo stage tracking by the scanner
- Supports use of advanced laser control features such as Position Synchronized Output and Analog Vector Tracking
- Optimize order of execution for combined motion paths with Aerotech’s CADFusion package
- Designed for use with Aerotech AGV galvo scanners; compatible with XY2-100 driven 3rd-party scanners
Aerotech’s Infinite Field of View (IFOV) is a unique and industry-leading solution for the synchronization of linear or rotary servo axes with laser scanners. IFOV produces significant throughput improvements and eliminates stitching errors and part quality issues due to overlapped and mismatched laser processing. By combining the high dynamic capabilities of galvo scanners with the travel range of servo stages, parts significantly larger than a scanner’s traditional field of view can be processed continuously with no need to stitch individual working areas together.
Infinite Field of View improves processing quality as well as throughput on large parts. IFOV not only expands the working area for any galvo system beyond what is possible with optics alone, but it also removes the trade-offs between laser spot size and available working area by extending the FOV regardless of optic selection. As a result, the user is able to select the best optic configuration for the job without compromising working area and therefore eliminates the need for a compromised solution.
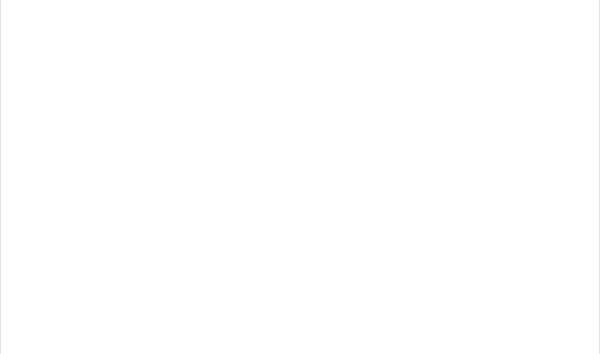
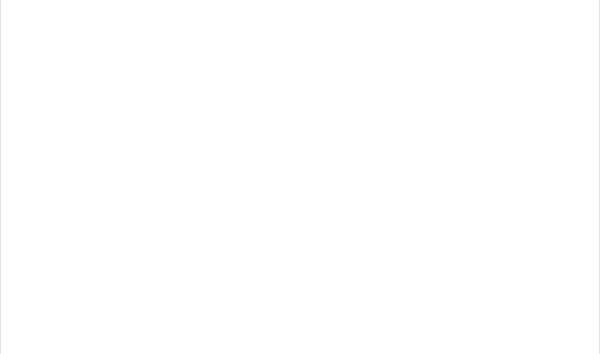
Effortless Operation
IFOV works every time without the user adjusting parameters and settings for different motion paths. This is because IFOV uses a single controller to process the user’s desired 2D profile and turn it into the relative servo stage and scanner motion in realtime. IFOV takes into consideration the scanner’s available working area to ensure its commanded trajectory stays within its field of view. It also takes into consideration the acceleration and current limits of both the servo and scanner axes so that the commanded motion will not cause fault conditions on either axes. All the while, the combined motion precisely maintains the user prescribed tool path.
Better Accuracy and Throughput
IFOV also leads to throughput improvements as well as accuracy improvements over similar solutions. Because IFOV uses a unified open control architecture, it shares actual feedback information across the controller, and makes it available to the user. As a result, the scanner’s motion includes the servo axes’ dynamic tracking error as part of its trajectory and corrects for it in real-time. This means that the user gets scanner-level dynamic tracking performance over the full part, regardless of using combined motion. It also means that the servo stages can be pushed faster and more aggressively without impacting the overall accuracy and quality of the finished part.
Compatible with Advanced Laser Control Features
Integrated feedback communication between drives allows for the creation and use of laser control features that are based on the actual tool-on-part position and velocity of the laser spot. Such features as Aerotech’s Position Synchronized Output (PSO) and Analog Vector Tracking functions allow the user to fire the laser as a function of tool position and modulate the laser’s power as a function of tool velocity.
Optimization of Combined Path with CADFusion
When performing motion profiles with a combined servo stage and scanner motion system, optimizing the order of execution for part features is critical to getting all of the benefits from the IFOV solution. Aerotech’s CADFusion 2D CAD/CAM software package has built-in optimization parameters that allow the user to plan their motion path for the most efficient feature execution order for any system. It also gives users the ability to influence how the IFOV algorithm separates the full motion profile between the two subsystems, and optimizes the path specifically for use with combined scanner and servo stage motion. CADFusion affords the user the ability to create, edit, hatch, optimize, and convert any vector-based CAD data into Aerotech executable G-code motion commands.
Works with All Aerotech AGV Products & XY2-100 Driven Scanners
The IFOV integrated controller feature works with all of Aerotech’s AGV family of galvo-scanner-based products. The realization of the benefits stems from a single controller and control architecture commanding both motion subsystems. However, it is possible to use Aerotech controls and take advantage of the IFOV controller feature with third-party stages and a scanner that accepts XY2-100 command communication. In the implementation of third-party equipment with Aerotech’s Automation1 controller, the servo loop of the scanner is self-contained within the third-party’s own drive hardware and not open to the Automation1 controller for interrogation. Therefore, the user loses the benefit of feedback integration across one controller. This means no servo stage dynamic error is corrected, and the real tool-on-part position and velocity of the laser spot is unknown. Other lost benefits are value adding laser control features such as Position Synchronized Output and Analog Vector Tracking. These shortcomings are also found in competitive solutions where different independent controllers are integrated together. Separately generating the servo and scanner trajectories while attempting to synchronize commands across disparate controllers will never work as well as a vertically integrated solution.