Aerospace & Defense, Capability Overview, Custom Engineered Motion Systems, Gantries, Gimbals & Optical Mounts, Hexapods, Integrated Automation Systems, Motors, Piezoelectric Nanopositioners, Process-Specific Products, Science & Research Institutions, Semiconductor, Stages & Actuators
Capability Overview
Engineering and Manufacturing Vacuum Capabilities
Aerotech’s vast application experience, unmatched product scope, and extensive engineering capabilities make us the partner of choice for vacuum-compatible motion systems. Since its inception, Aerotech has designed and manufactured the highest-performance motion control and positioning systems available and our vacuum-compatible platforms are no exception. Aerotech has been building standard and custom vacuum systems for more than 30 years. Our vacuum application experience covers military/aerospace, research, semiconductor, and materials processing. Typical applications include:
- EUV Lithography
- Scanning Electron Microscopy (SEM)
- Ion-Beam Profiling
- Deposition
- Satellite Component Testing
- Transmission Electron Microscopy (TEM)
- Ion Implantation
- Optics Polishing
- Scientific Research
- X-Ray Tomography
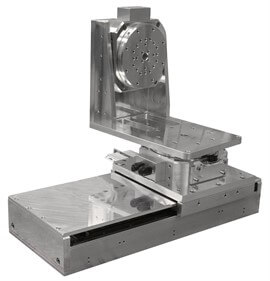
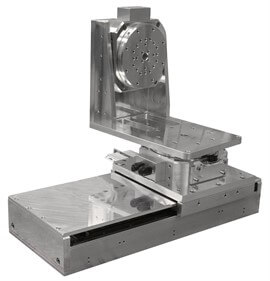
ALS20000/ADRS‑150/ADRS‑150
Vacuum Engineering Expertise
Our extensive testing capabilities provide full qualification of motion systems prior to shipment. Aerotech is a highly-integrated motion system supplier — we are able to fully optimize the complete motion system. For high-dynamic systems, Aerotech has several active cooling options that are based on thermal modeling and practical experience.
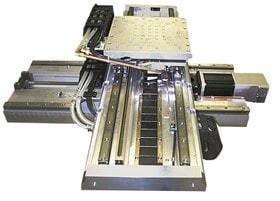
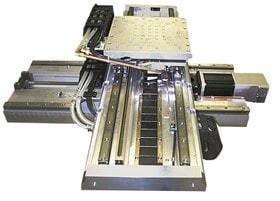
For applications that are sensitive to magnetic fields, Aerotech has extensive experience with methods for magnetic field shielding and containment. Aerotech’s talented and dedicated engineering staff has expertise in all core motion technology areas:
- Precision Machine Design
- Vibration and Controls
- Magnetic Circuit Design
- Power Electronics Design
- Servo Systems
- Software Development
Facilities for Vacuum Manufacturing
Aerotech has an extensive manufacturing facility that includes an ISO Class 6 cleanroom that is the ideal controlled environment for building UHV systems. Our machine shop is fully qualified to manufacture vacuum compatible components. We maintain a vacuum test chamber, full on-site part cleaning facilities, and fully-trained assembly and test staff.
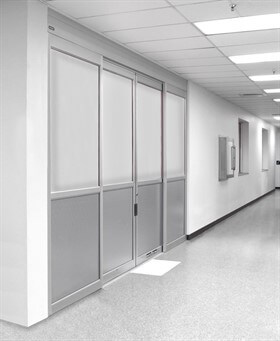
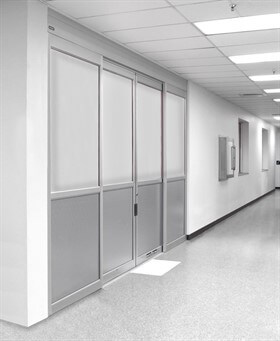
Vacuum Staging Design Elements
A wide variety of standard Aerotech stage products are available in vacuum-prepared versions. In addition to standard platforms, Aerotech routinely manufactures custom systems designed to meet application specific needs. All of Aerotech’s vacuum-compatible motion platforms minimize pumpdown time, chamber contamination, and thermal issues. In addition, these systems can incorporate key application considerations like reduction of magnetic fields.
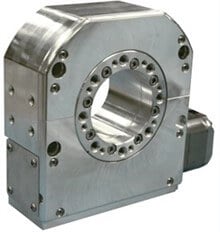
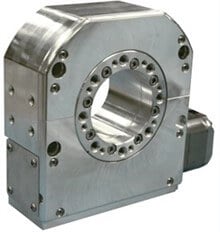
Aerotech is well versed in:
- Material Selection
- Surface Preparation
- Elimination of Virtual Leaks
- Lubricant Selection
- Cleaning
- Bakeout
- Handling
- Thermal Management
- Magnetic Field Control
- Packaging
Vacuum Options Available From Aerotech
Level | Torr | mBar | kPa |
Low Vacuum (VAC3) | 1.0 x 10-3 | 1.3 x 10-3 | 1.3 x 10-4 |
High Vacuum (VAC6) | 1.0 x 10-6 | 1.3 x 10-6 | 1.3 x 10-7 |
Ultra-High Vacuum (UHV) | ≤1.0 x 10-7 | ≤1.3 x 10-7 | ≤1.3 x 10-8 |
Material Selection
Because acceptable materials vary according to vacuum level, application, operating temperature, etc., Aerotech offers a broad array of options that control Total Mass Loss (TML) and Collectible Volatile Condensable Materials (CVCM).
- Lubricants: Low vapor pressure lubricants are selected to be compatible with the vacuum level and the customer’s process.
- Cable Management System (CMS): CMS construction and materials typically utilize Teflon® insulated wires (MIL-C-27500) or Kapton along with specialized electrical connectors that utilize a variety of materials including PEEK™. A multitude of connectorization options are available.
- Surface Finish: Surface finish options include bare aluminum, electroless nickel, stainless steel, or vacuum-compatible paint (Aeroglaze Z306).
- Hardware: Systems use through-holes or vented stainless-steel fasteners for all blind holes.
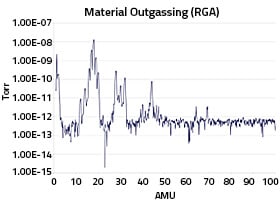
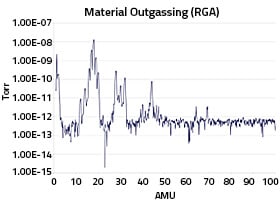
Aerotech always works closely with our customers to ensure the system meets or exceeds outgassing requirements.
Thermal Management
Thermal management is key in vacuum systems because they cannot rely on convection for the removal of heat from the motors and bearings. Without thermal management methods, stage performance suffers and life can be reduced from that of an equivalent system operated in atmosphere. This is why Aerotech has put forth a considerable effort in the development of thermal isolation methods and passive and active cooling techniques. These techniques help to maximize conduction and radiative modes of cooling and help reduce or eliminate the effects of heat sources inside the chamber.
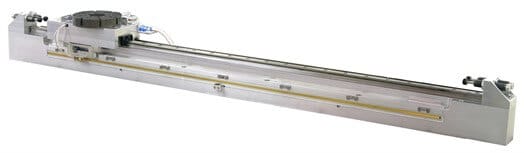
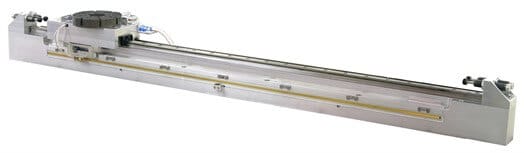
Servomotors
The design of linear and rotary servomotors is critical to vacuum system operation because they are the primary heat source. This is why Aerotech designs and builds motors to specifically address the issues associated with motors in vacuum. From special materials of construction to magnetic circuit design, Aerotech servomotors are optimized for minimal outgassing, high force/torque per unit volume, and long life.
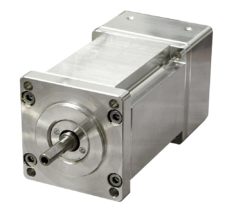
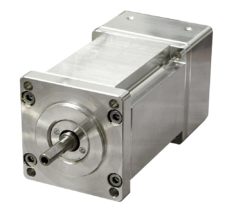
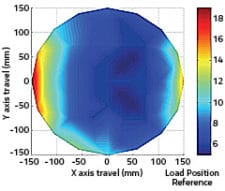
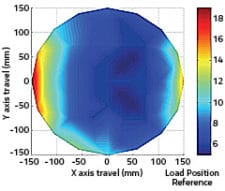
Extensive Motor Options
Aerotech’s complete line of vacuum stages incorporate drive technologies that span piezos, rotary stepper, rotary servo, linear, and curvilinear motors. Our direct-drive solutions extend machine dynamic performance while at the same time minimizing contamination due to their noncontact design. Special motor designs and shielding are available to attenuate stray magnetic fields in sensitive applications.
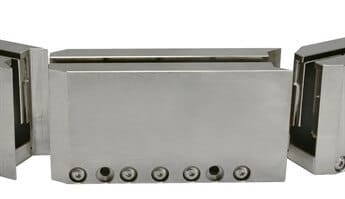
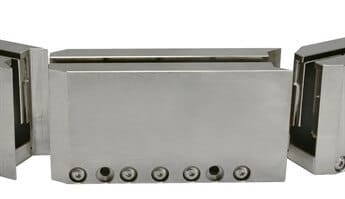
Tuning and Troubleshooting
Aerotech controllers provide extensive diagnostics to allow tuning and troubleshooting the motion system without opening the vacuum chamber. Data acquisition includes position, velocity, current, and frequency response plots, as well as the ability to do FFT.
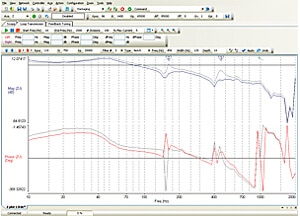
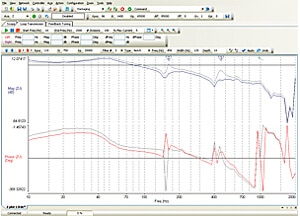
Feedforward Interface with Isolation Systems
Options are available to allow direct communication of motion commands between the Aerotech controller and an active isolation system. Isolation feedforward dramatically reduces stage-induced vacuum chamber motion, thereby increasing system throughput.
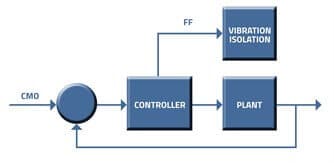
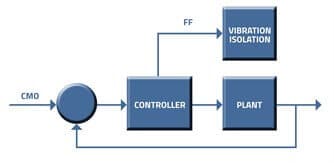
Automation1 Motion Controller and Drives
The Automation1 precision motion control platform includes a powerful motion controller and servo motor drives that provide optimum performance for your vacuum system. The multi-axis machine controller is software-based and is designed to be deployed either to an industrial PC or on an embedded processor running on specific Automation1 drive-based controller hardware. Powerful HMI tools including the MachineApps HMI builder and .NET, C, and Python APIs enable users to combine vision systems, PLC control, robotic controllers, and world class motion control in one powerful solution. The Automation1 AeroScript real-time programming language enables process control to be tied tightly to your system’s precision motion. The controller communicates with precise Automation1 servo motor drives over the ultra-fast HyperWire glass-optical-fiber motion bus, sending high-resolution motion trajectories to each servo drive. Standard, low-noise linear amplifier servo drive and custom configurations are also available.
Aerotech Advanced Controls
Dramatically improve your vacuum system’s motion performance with Aerotech’s Dynamic Controls Toolbox (DCT). The DCT provides control algorithms that increase system performance such as settle time, accuracy, in-position stability, and/or velocity stability. These include Harmonic Cancellation, Threshold, Dynamic Gain Scheduling, Command Shaping, and Cross-Axis Feedforward. Aerotech controllers also provide a direct feedforward interface to chamber active isolation systems.
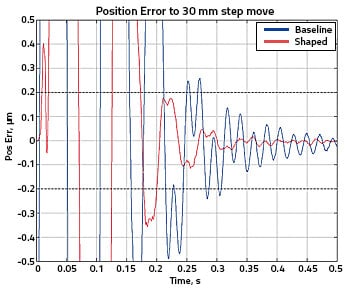
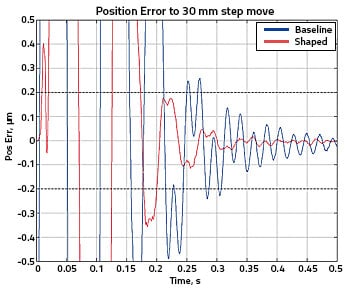
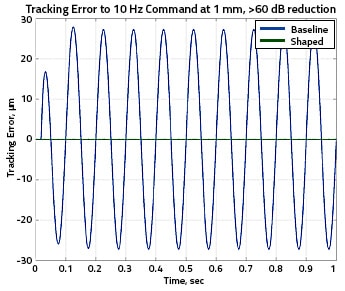
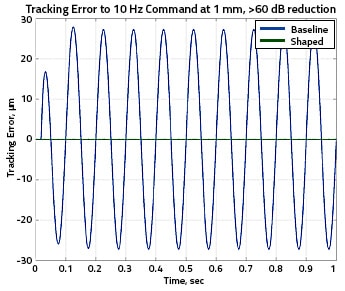
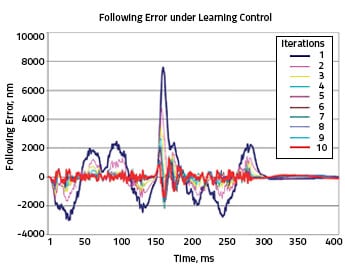
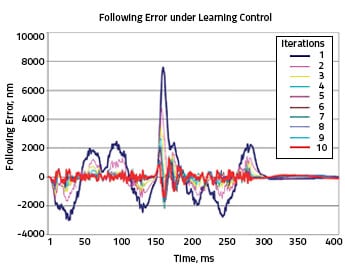
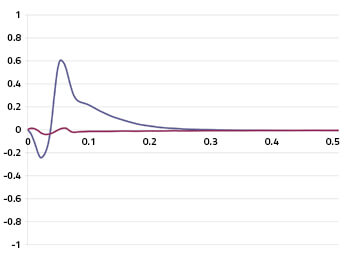
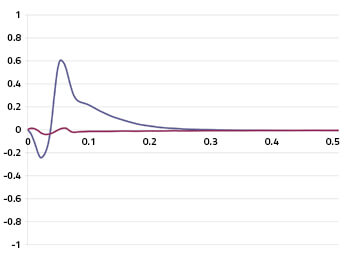
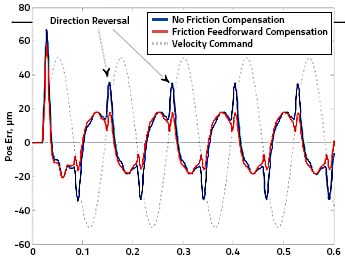
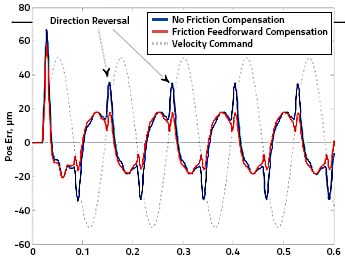
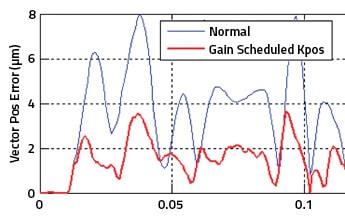
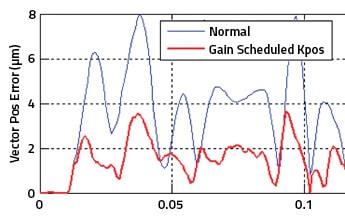
Magnetic Field Management
Certain vacuum applications require very low magnitude magnetic fields as well as minimal field fluctuation at the system work point. Existence of either of these conditions can cause process related problems. Aerotech addresses these “AC” and “DC” field issues through use of specialized shielding techniques, special magnet track design and use of nonmagnetic materials. In addition, the mechanical system is designed to keep the motor coils and magnets well away from process work points.
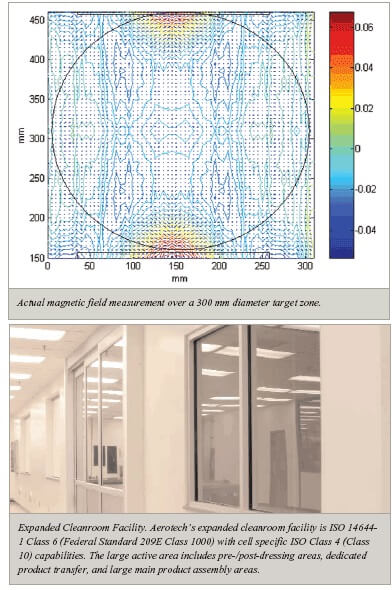
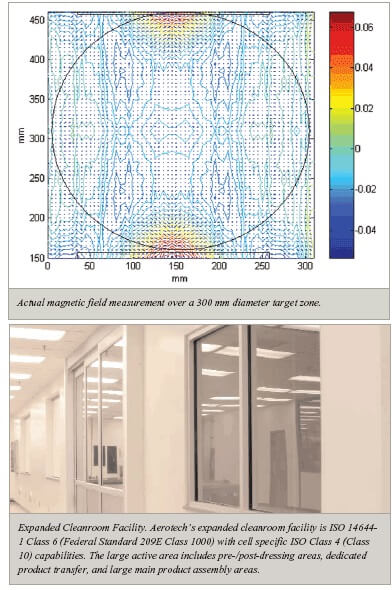
Handling/Cleaning
Handling is critical in maintaining the integrity of a vacuum stage system. Vacuum systems are assembled in Aerotech’s expansive cleanroom by precision assemblers wearing polyethylene, powder free gloves. All parts are thoroughly cleaned to remove oils and other contaminants. Following cleaning, components are packaged in heat-sealed nylon or particle-free polyethylene bags. Where required, component-level bake-out is available. For more information regarding Aerotech’s Vacuum Advantage, please contact a member of our knowledgeable sales staff.
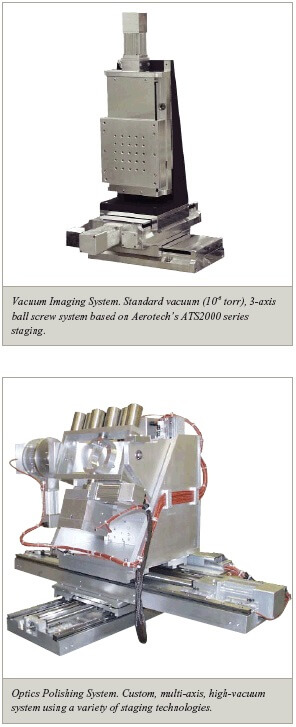
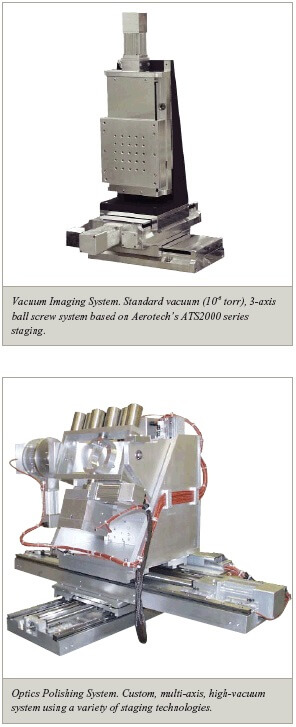
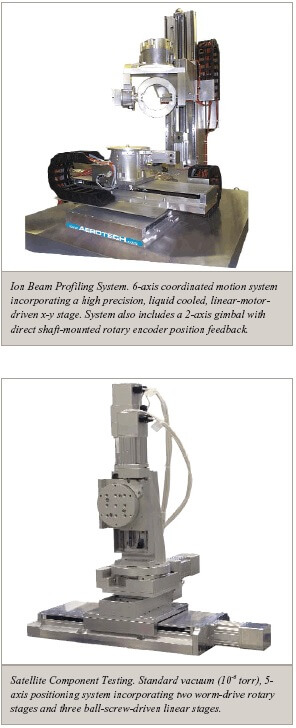
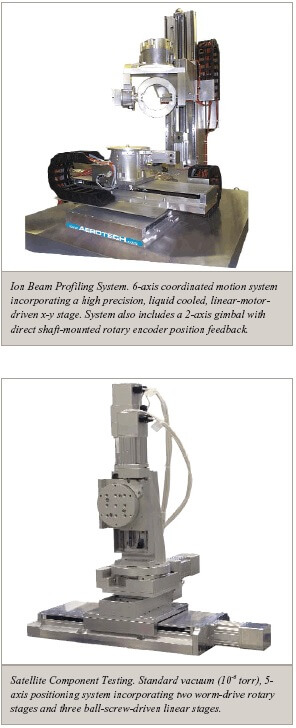